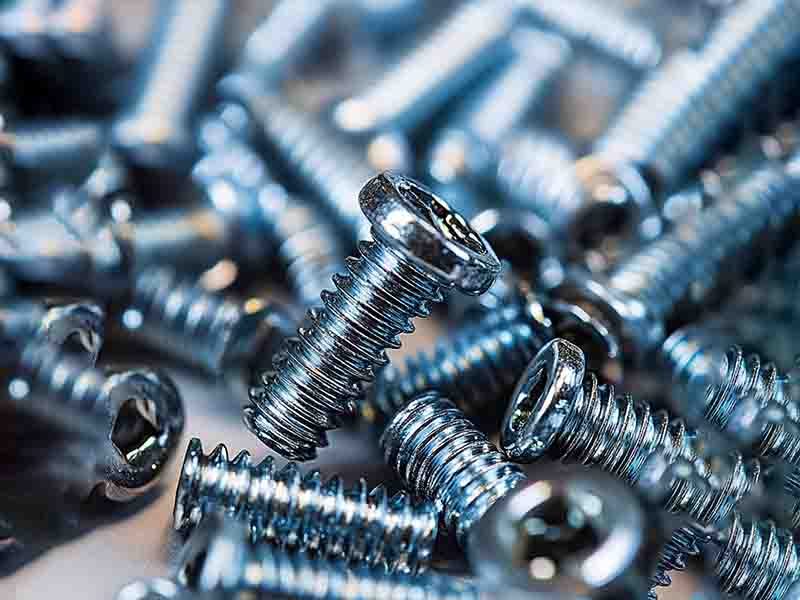
Table of Contents
1. Wire Preparation: Laying the Foundation for Quality
The manufacturing process begins with the selection of the right wire. This is a crucial first step, as the type of wire chosen determines the overall strength, durability, and functionality of the screw. Common materials include:
- Carbon Steel: Ideal for general-purpose screws that require good strength and durability.
- Stainless Steel: Best for applications where resistance to corrosion is a priority.
- Copper: Often used in electrical components for its excellent conductivity.
- Aluminum: Chosen for its lightweight properties in industries where weight reduction is essential.
The diameter and material of the wire are chosen based on the specific specifications and intended use of the screw. For example, screws used in construction might require a thicker wire, while screws for delicate electronic devices might require a thinner wire. Once the appropriate wire is selected, it is cut to the required length and prepared for the next step in the process.
2. Cold Heading: Shaping the Screw Head
The second step in screw manufacturing is cold heading, a process that involves shaping the wire into the desired screw head at room temperature. This is done using a punch to deform the wire, forming the head of the screw.
During this step, the wire is placed into a machine with a die that molds the wire into the head shape. The head of the screw can take various forms, including:
- Flat Head: Commonly used in wood screws, where the head sits flush with the material surface.
- Round Head: Typically used in applications where the screw needs to be visible or provide extra strength.
- Pan Head: Often seen in electronic devices and appliances for a smooth finish.
Cold heading is crucial because it determines not only the shape of the screw’s head but also its strength. By using cold heading, the material is compressed, which helps to increase its strength and integrity.
3. Thread Rolling: Creating Precision Threads
One of the most critical stages in screw manufacturing is thread rolling. This process involves passing the screw through two rotating dies, which contain the negative shape of the thread. As the screw moves through the dies, the material is squeezed and compressed to form precise threads.
Why is thread rolling so important? Unlike traditional methods of cutting threads, thread rolling enhances the strength and precision of the screw. The rolling process does not remove material, meaning the threads are not weakened, resulting in screws that are stronger and more durable. This is particularly important for applications where screws are subjected to high stress or need to withstand harsh conditions.
In addition to improving strength, thread rolling also enhances the precision of the screw’s threads, ensuring a perfect fit every time. Whether the screw is meant for a delicate application or heavy-duty use, thread rolling guarantees that the threads are consistent and capable of holding the materials together securely.
4. Heat Treatment: Ensuring Strength and Durability
After the screw has been cold-headed and threaded, it undergoes heat treatment to improve its hardness and strength. This process involves heating the screw to a specific temperature and then rapidly cooling it, typically through quenching in oil or water. Heat treatment ensures that the screw can withstand the stress it will encounter in its intended application, making it stronger and more resistant to wear and tear.
Heat treatment also plays a key role in improving the corrosion resistance of screws, particularly those made of carbon steel. The treatment process can be tailored to meet the specific requirements of the material, ensuring the final product meets the necessary performance standards.
5. Finishing: Adding the Final Touches
The final step in the screw manufacturing process is the finishing stage. This includes a variety of operations such as:
- Polishing: To create a smooth, shiny surface, especially for screws used in visible areas like electronics or decorative hardware.
- Coating: Applying coatings such as zinc, nickel, or chrome for enhanced corrosion resistance, especially for screws used outdoors or in environments exposed to moisture.
- Trimming: Ensuring the screw is cut to the correct length and that any excess material is removed.
At this stage, screws are also subject to quality control checks to ensure that all dimensions, threads, and material properties meet the required standards. This is a vital step to guarantee that the screws perform reliably when put to use.
6. Packaging and Shipping: Ready for the Market
Once all the processes are complete, the screws are carefully packaged and shipped to customers worldwide. Depending on the customer’s requirements, screws can be packaged in bulk for industrial use or in smaller quantities for retail sale.
In Conclusion, the screw manufacturing process is a highly detailed and technical procedure that ensures each screw meets the stringent quality standards required for its end use. From selecting the right material to shaping, threading, heat treating, and finishing, each step plays a crucial role in creating a strong, durable, and precise product. By understanding these steps, businesses can ensure they select the right screws for their applications, helping to prevent costly mistakes and ensuring the success of their projects.
Why Choose FHT for Your Screw Manufacturing Needs?
At FHT, we take pride in our rigorous screw manufacturing process, ensuring that every screw we produce meets the highest standards of quality and precision. Whether you need standard screws or custom-designed fasteners, we have the expertise and capabilities to deliver solutions that meet your needs. Our commitment to quality assurance, fast delivery, and customer satisfaction makes us the ideal partner for all your screw manufacturing needs.
Contact us today to learn more about our manufacturing process and how we can help you with your next project.