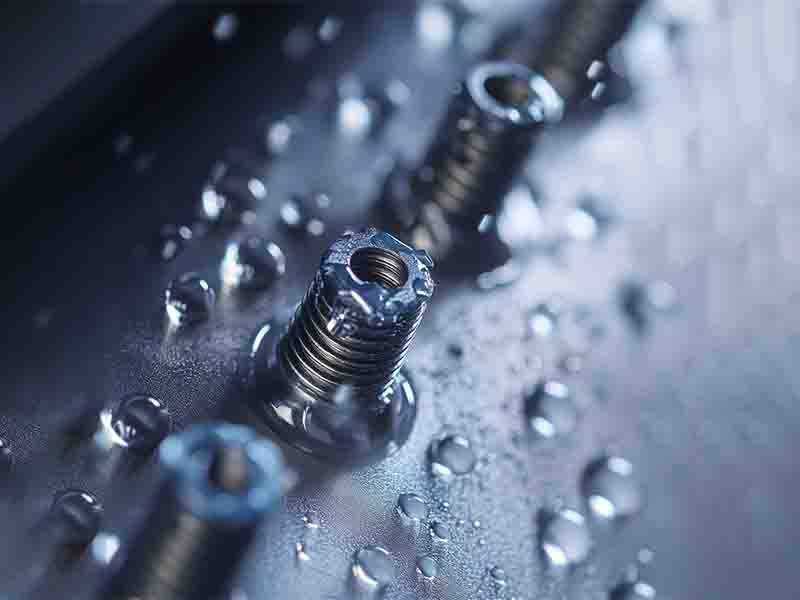
Table of Contents
What Is a Salt Spray Test?
The salt spray test is a widely used corrosion testing method that measures a screw’s resistance to corrosion. By simulating high-salinity environments, the test allows manufacturers to observe how quickly screws corrode under harsh conditions and assess their anti-corrosion performance.
Why It Matters: Corrosion can compromise the strength and lifespan of screws, especially in marine environments or high-humidity conditions. The salt spray test ensures that screws meet durability standards for demanding applications.
Principle of the Salt Spray Test
The test creates a controlled salt spray environment inside a closed test chamber. Using a 5% sodium chloride solution, the salt spray is atomized and sprayed onto the screws to replicate the corrosive conditions found in coastal or high-salinity environments.
How It Works:
- The screws are exposed to highly concentrated salt mist at a set temperature and humidity.
- Over time, the screws show varying degrees of corrosion, which are then analyzed to determine their resistance levels.
Example: A screw designed for outdoor use must resist rust when exposed to humid or salty air, like in coastal construction projects.
Steps of the Salt Spray Test
-
Prepare Samples
- Select screws to be tested and ensure their surfaces are clean and free from oil or contaminants.
-
Set Up the Salt Spray Chamber
- Add a 5% sodium chloride solution to the chamber.
- Adjust the chamber temperature to approximately 35°C and maintain a relative humidity above 95%.
-
Place the Samples
- Position the screws inside the test chamber, ensuring they do not touch the walls and are fully exposed to the salt spray on all surfaces.
-
Set the Test Duration
- Determine the required testing time based on standards or application needs.
- Common durations include 24 hours, 48 hours, 72 hours, or longer for highly demanding applications.
-
Observe and Record Results
- After the test, remove the screws, clean and dry them, and carefully observe the extent of corrosion.
- Record any visible rust, discoloration, or pitting.
Standards for Salt Spray Testing
Salt spray tests follow specific international and national standards to ensure consistency and reliability. The most common standards include:
-
- The most widely used salt spray test standard, outlining operating conditions and test procedures in detail.
-
- A globally recognized standard developed by the International Organization for Standardization for salt spray testing.
-
GB/T 10125
- The Chinese national standard, which specifies the test methods and requirements for evaluating corrosion resistance.
Why Standards Matter: Using these standards ensures that results are consistent, comparable, and meet industry requirements, no matter where the screws are tested or used.
Conclusion: Why Is the Salt Spray Test Important?
The salt spray test plays a vital role in assessing the durability and corrosion resistance4 of screws and other fasteners. By simulating real-world corrosive conditions, manufacturers can:
- Identify weak points in materials or coatings,
- Improve product quality and longevity,
- Ensure screws meet industry standards for performance and reliability.
At FHT, we take corrosion resistance seriously. Our screws undergo rigorous salt spray testing to ensure they can withstand harsh environments and deliver long-lasting performance. Whether for construction, automotive, or marine applications, our products are designed to excel under pressure.
Looking for corrosion-resistant screws that meet global standards?
Contact us today to request a sample or discuss your project needs!
Footnotes
- Salt spray test: Overview of the process for evaluating corrosion resistance in screws.
- ASTM B117: The most widely adopted standard for salt spray corrosion testing.
- ISO 9227: International standard for salt spray tests, ensuring global consistency.
- Corrosion-resistant applications: Common uses for screws in marine, automotive, and construction industries.