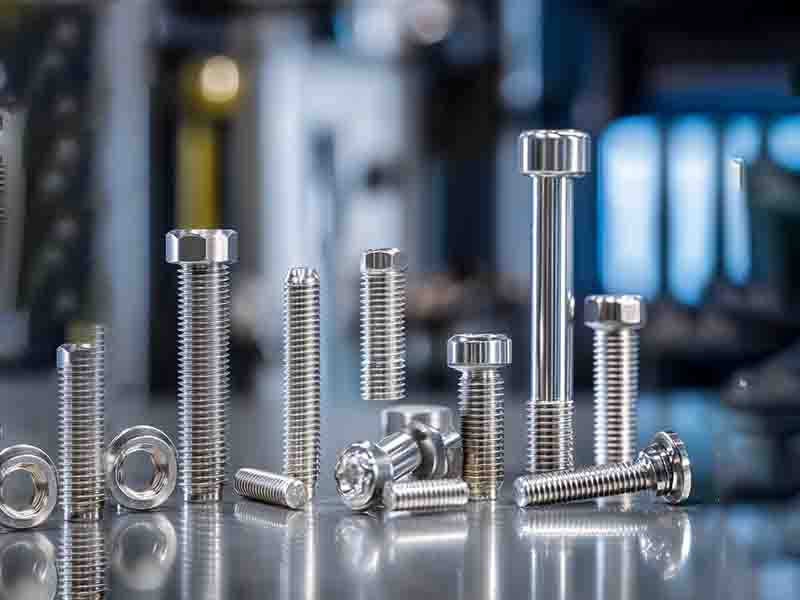
Choosing the correct screw specifications is essential to ensuring secure, long-lasting, and efficient fastening in any application. To make the right choice, several critical factors must be considered based on the requirements of your specific project. Here’s a practical guide to help you select the perfect screws for your needs.
Table of Contents
1. Load Requirements
Why It Matters: Screws must have sufficient strength to withstand the mechanical load they will experience during use.
- Consider the Strength Grade1:
Screws come in various strength grades (e.g., 4.8, 8.8, 10.9, or 12.9 for metric screws). Higher numbers indicate greater tensile and shear strength. - Application Tip: For heavy-duty industrial applications or structural assemblies, select screws with a higher strength grade to ensure reliability.
Example: A structural steel connection requires high-strength screws like grade 10.9 to handle significant loads safely.
2. Environmental Conditions
Why It Matters: Environmental factors such as humidity, exposure to chemicals, or corrosive atmospheres can affect screw performance and durability.
- Stainless Steel Screws2: Ideal for humid, outdoor, or corrosive environments because of their superior resistance to rust. Grades such as 304 or 316 stainless steel offer excellent corrosion resistance.
- Galvanized Screws: A cost-effective option for moderate protection against corrosion. These screws are coated with a layer of zinc to prevent rusting.
Example: In marine environments, screws made from 316 stainless steel are preferred because of their exceptional resistance to saltwater corrosion.
3. Assembly Requirements
Why It Matters: The head shape3 and thread type4 of a screw determine its compatibility with tools and the specific application.
-
Head Shapes:
- Hex Head: Provides high torque capability, ideal for industrial applications.
- Flat Head: Sits flush with the surface, suitable for applications requiring a smooth finish.
- Round Head: Commonly used when a decorative, raised finish is desired.
-
Thread Types:
- Coarse Threads: Faster to install and ideal for softer materials like wood or plastic.
- Fine Threads: Provide better grip in harder materials such as metal and offer greater resistance to loosening under vibration.
Example: For assembling wooden panels, flat-head wood screws with coarse threads ensure a clean, flush connection.
4. Dimension Requirements
Why It Matters: The length and diameter of a screw are crucial to ensure it fits the application properly.
- Length: Select the screw length based on the thickness of the workpiece and assembly position. The screw should penetrate the material sufficiently for a secure hold without overextending.
- Diameter: Choose the screw diameter to match the load-bearing requirements and the size of the drilled hole.
Rule of Thumb: The screw should be twice as long as the material thickness for optimal grip and strength.
Example: If fastening a 10mm thick metal plate, a screw length of approximately 20mm is ideal for a secure connection.
Conclusion: Selecting the Right Screw for Success
Selecting the correct screw involves evaluating the load requirements, environmental conditions, assembly needs, and dimensional specifications. By considering these factors, you can ensure reliable performance, durability, and safety in any application.
At FHT, we offer a wide variety of screws tailored to meet your project needs. From high-strength industrial fasteners to corrosion-resistant stainless steel options, our products guarantee performance and quality.
Need help selecting the right screws for your application?
[Contact us today for expert advice and custom solutions!]
Footnotes
- Strength Grades: Understanding the tensile strength and load capacity of screws (e.g., 8.8, 10.9).
- Stainless Steel Screws: Explains 304 vs. 316 stainless steel for corrosion resistance.
- Screw Head Shapes: Overview of head types and their ideal applications.
- Thread Types: Comparison of coarse and fine threads for different materials.